Extensive Product Lifecycle Support for Semiconductor Equipment
Onsite field service engineers, technical support and depot repair services for semiconductor manufacturing and test equipment — leveraging advanced tools, deep technical expertise and a cleanroom environment
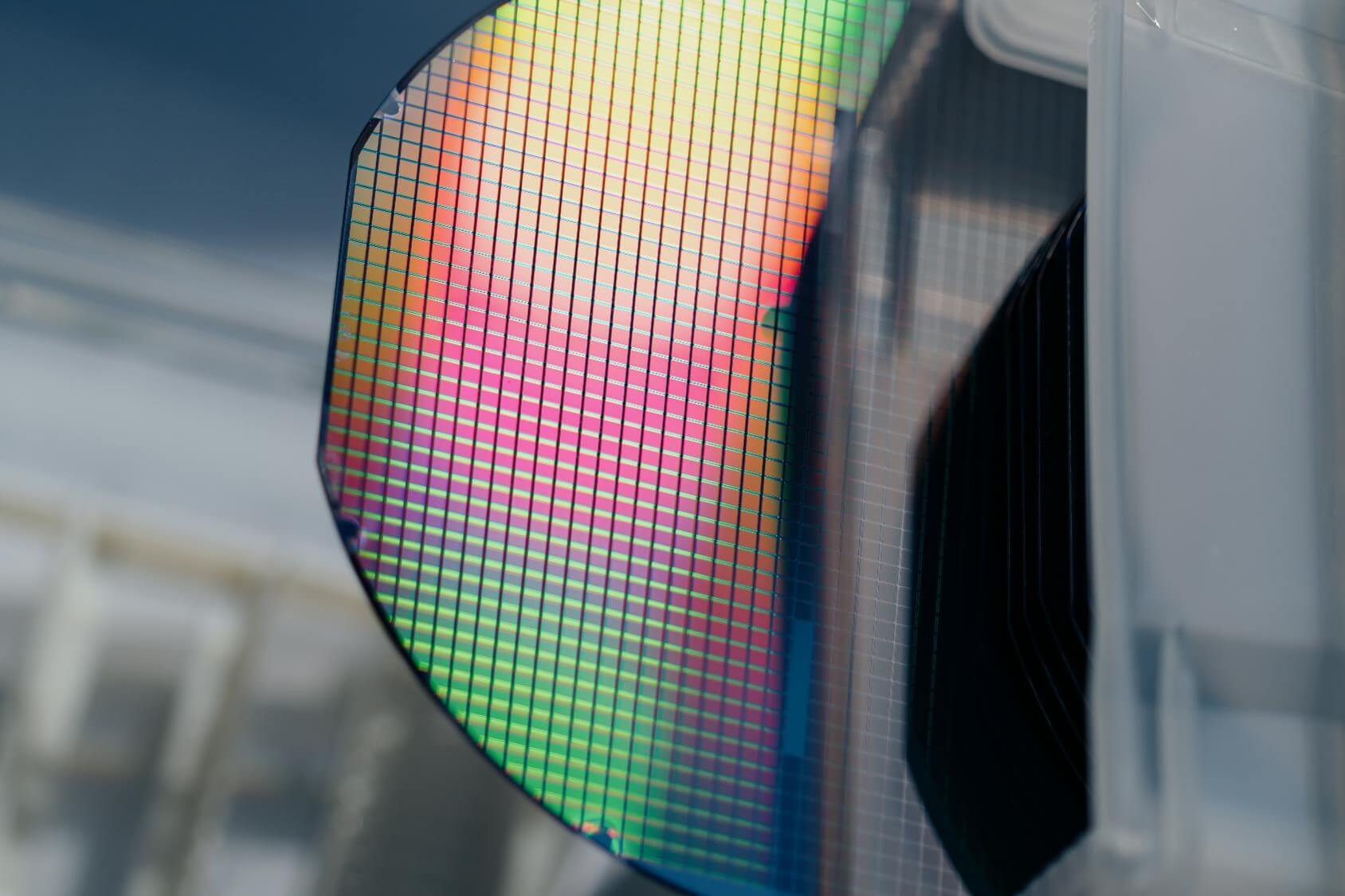
Complex Equipment Calls for Uncompromising Services and Support
The equipment used in semiconductor manufacturing is highly sophisticated, including lithography systems, deposition equipment, etching machines, inspection and metrology tools, and other precision instruments. Miniaturization, heterogeneous integration and advanced packaging are driving the need for enhanced knowledge, tools and processes, while supply chain constraints, environmental regulations, skilled labor shortages and other challenges threaten the ability of original equipment manufacturers (OEMs) to meet customer expectations.
Repairing and servicing semiconductor equipment flawlessly requires equally sophisticated services as well as a high level of expertise to address increasing complexity in a technologically sophisticated and rapidly evolving industry. Keep your high-value semiconductor manufacturing equipment in service and operating at peak performance longer with a proven outsourced services partner like Shyft Global Services.


Refocus on Innovation That Keeps You Competitive
Outsourcing your semiconductor equipment services to a partner with the knowledge, processes and capabilities to manage them meticulously garners key business and technical outcomes for you and your customers:
Optimal Quality and Support
Deliver an elite customer experience with a semiconductor equipment services partner dedicated to uncompromising quality, continuous improvement and high standards for ongoing support
Enhanced Sustainability
Outsourcing services to a sustainability-minded partner can simplify lifecycle management and help your organization meet stringent regulatory requirements without compromising performance
Data and IP Protection
Protect vulnerable assets with robust security and data handling protocols that ensure private, proprietary and sensitive information stays that way for semiconductor manufacturing equipment while it’s in transit and being serviced
Efficiency and Uptime
Increase uptime and minimize production disruption with technology services that marry expertise and experience with OEM-authorized component sourcing, deep supply chain relationships and superior inventory management
Outsourced Technology Services for Semiconductor Equipment Manufacturers
-
Outsourced Technology Services for Semiconductor Equipment Manufacturers
Depot Repair
Repairing semiconductor manufacturing equipment requires deep expertise, a deft hand and the right tools and processes to meet industry standards, maintain quality and prevent recurring issues in a sector where precision and uptime are paramount.
Shyft’s equipment testing facilities, high-tech integration labs and global repair depots are compliant with numerous industry standards and meet the high level of strict controls unique to semiconductor equipment manufacturing. Shyft’s depot repair capabilities include:
- Component-level repair
- Root cause analysis
- Technical engineering
- Quality testing
- Logistics management
- Sustainability support
- Situational solutions
- Cleanroom environment
- 3D X-ray capability for BGA solderability assessment
- Unique semiconductor equipment repair, such as:
- Custom PCBA assemblies, power supplies and compute devices
- High precision motors
- Precision mechanical measurement capability
Supply Chain Management
Global supply chain and inventory management expertise is a de facto requirement for any partnership that relies on the availability of electronic components, as are rock-solid relationships and contingency plans with the companies that make them. Shyft’s supply chain experts and flexible supply chain solutions help to optimize and streamline the supply chain for semiconductor equipment manufacturers. Capabilities include:
- Inventory management
- Forecasting and replenishment processes
- Secure product warehousing and distribution
- Fulfillment centers around the world
- Import/export management
- Returns administration
- Transportation management
- White-glove delivery
- RMA handling
- Inspection and testing
- Financial services
- E-commerce
- Pricing and promotions
- Pre- and post-sales support
Global Field Services
While some semiconductor manufacturing equipment or components require the strictly controlled environment of a cleanroom, other types of equipment need onsite support. Shyft’s global network of trained engineers and white-labeled global field services help ensure your equipment is properly deployed, maintained and supported for consistent, long-term use. Global field service capabilities include:
- Spare parts management
- Installation and implementation
- Deployment
- Warranty monitoring and management
- RMA management
- 24x7 onsite response
- 24x7 Global Technical Assistance Center (GTAC) and help desk
- Remote diagnostic support
- Onsite diagnosis of failed equipment down to field replaceable unit (FRU)
- Maintenance and support for:
- All in- and out-of-warranty maintenance
- End-of-life product support
Technical Support
Grow your technical coverage and keep your equipment running optimally through Shyft’s combination of technical expertise, product parts and labor. Our experienced team is trained to work with semiconductor manufacturing equipment and respond to customer support requests quickly. Technical support coverage may include:
- L1–L3 engineering and technical expertise
- 24x7x365 Global Technical Assistance Center (GTAC)
- Essential troubleshooting
- Case escalation and resolution
- Engineering staff augmentation
- Pre-sales engineering
- ECO/FCO management
- Parts planning, dispatch and asset recovery
- Onsite coordination and day-of support
- End-of-life and recall management
Customer Management
Shyft’s technology services support extends to the customer lifecycle, too. With our custom-built, cost-effective, white-label customer management solutions, you can more easily garner additional expansion and revenue opportunities. Shyft’s global customer management capabilities include:
- Multilingual support
- Renewals management
- Relationship management
- Upgrades, upsells and cross-sells
- Revenue expansion
- Net-new opportunities identification
- Channel partner programs
- Surveys and customer touchpoints
- Education and training
- In-house Business Intelligence (BI) unit
Solving Key Repair and Service Challenges for Semiconductor Equipment Manufacturers
Semiconductor manufacturing demands precisely engineered, meticulously calibrated and technologically sophisticated equipment at every step of production. The complexity of manufacturing devices, instruments and processes, along with trends such as miniaturization and heterogeneous integration, are driving the need for equally advanced knowledge, tools and procedures to keep high-value equipment in service and operating at peak performance long after initial deployment.
Mastery across technologies, systems and protocols — combined with a focus on quality and compliance — means you can rely on Shyft to service your most complex and precisely calibrated semiconductor manufacturing equipment.
Extend Your Reach With Shyft’s Established Global Infrastructure
Shyft’s global infrastructure spans over one million square feet in every region of the world — with state-of-the-art facilities and processes that allow semiconductor equipment manufacturers to modernize their logistics network and deliver customer excellence seamlessly.
-
Our geographic footprint spans the globe, enabling more robust collaboration opportunities with customers, partners, integrators and suppliers to maximize the potential of technology for everyone. Our key global facilities include:
- Groveport, Ohio: 586,000 sq. ft.
- Roseville, California: 220,000 sq. ft.
- Warsaw, Poland: 178,820 sq. ft.
- Tiel, Netherlands: 63,000 sq. ft
- Tampines, Singapore: 22,500 sq. ft.
-
With a single provider like Shyft who offers flexible supply chain solutions and follows best practices for supply chain resiliency, semiconductor equipment manufacturers can consolidate their end-to-end logistics processes and deliver a seamless experience through our well-established, time-tested global infrastructure. A streamlined supply chain and optimized inventory management can reduce overhead costs and scale effortlessly as technologies and customer requirements shift.
-
Cleanroom protocols are some of the most stringent and explicitly followed in the technology manufacturing industry and require significant investment in air filtration and HVAC systems, temperature and humidity controls and other environmental controls. Shyft operates a cleanroom to ISO 5/Class 100 standards in California with top-of-the-line infrastructure in place to handle the intricacies of depot repair work required for vulnerable, often complex semiconductor manufacturing equipment.
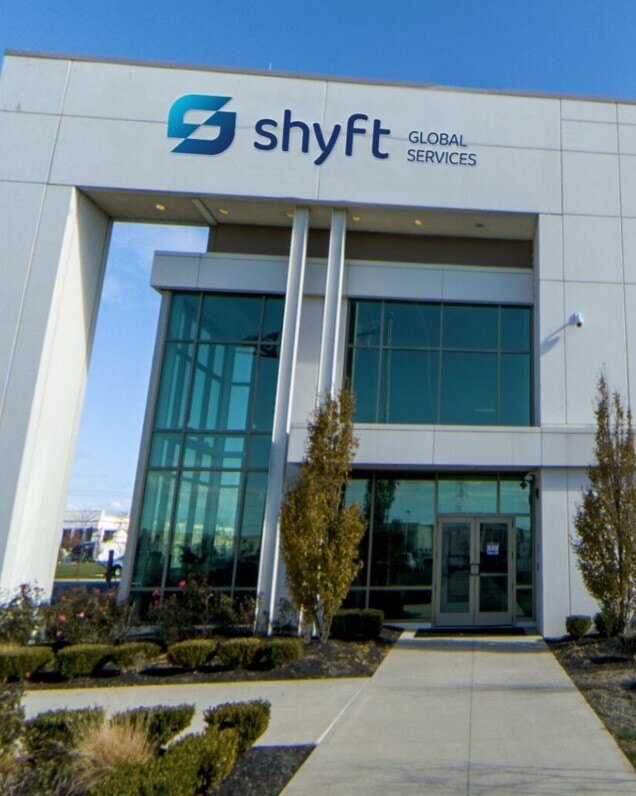
Global Sustainability Support for Semiconductor Equipment
Demand for an eco-conscious closed-loop system in which equipment is designed, produced, consumed and recycled with minimal waste and maximum reuse is on the upswing. Participation in the circular economy is key to manufacturers looking for ways to reduce costs, boost revenue, ensure compliance and enhance their commitment to corporate sustainability.
Choosing a partner who shares your company’s commitment to sustainability and compliance is a fiscally sound decision that resonates positively with suppliers, customers and investors alike.
-
With consumers, governments and business partners demanding the adoption of eco-conscious practices, semiconductor equipment manufacturers are held to ever-higher standards for sustainability and environmental compliance. Contributing to the circular economy can lead to profitable opportunities throughout the product lifecycle, and protecting the environment gives your company a poignant story to tell. Just be sure to follow through on your sustainability commitment.
-
Well-engineered semiconductor manufacturing equipment is likely to outlast the lifespan of the components comprising it. An effective repair strategy ensures that equipment is back in service quickly and environmentally sound processes are in place to dispose of parts that are defective, technologically outdated, physically damaged or have been deemed unreliable for whatever reason.
-
A wide range of tools and machines lend themselves well to the outsourcing depot repair center model. But due to the size of certain pieces of semiconductor equipment and the complexities of operating in a cleanroom, the most common model for larger equipment is to have onsite field technicians diagnose the failed equipment down to the field replaceable unit (FRU). The FRU is then sent to the repair service partner to perform an assessment, diagnostic, repair and thorough testing.
-
With best-in-class expertise, capabilities, relationships and global locations, Shyft provides sustainability and circular economy support from product design to end-of-life disposal, helping OEMs find the right balance between environmental responsibility and corporate profitability.
Thoughtful, proactive decisions about materials, components and distances centered on environmental, social and governance (ESG) considerations can move the needle in meaningful ways. Further, reusing, repairing and recycling materials and components whenever feasible can offer fiscal advantages in terms of on-hand replacement parts and incremental revenue opportunities.
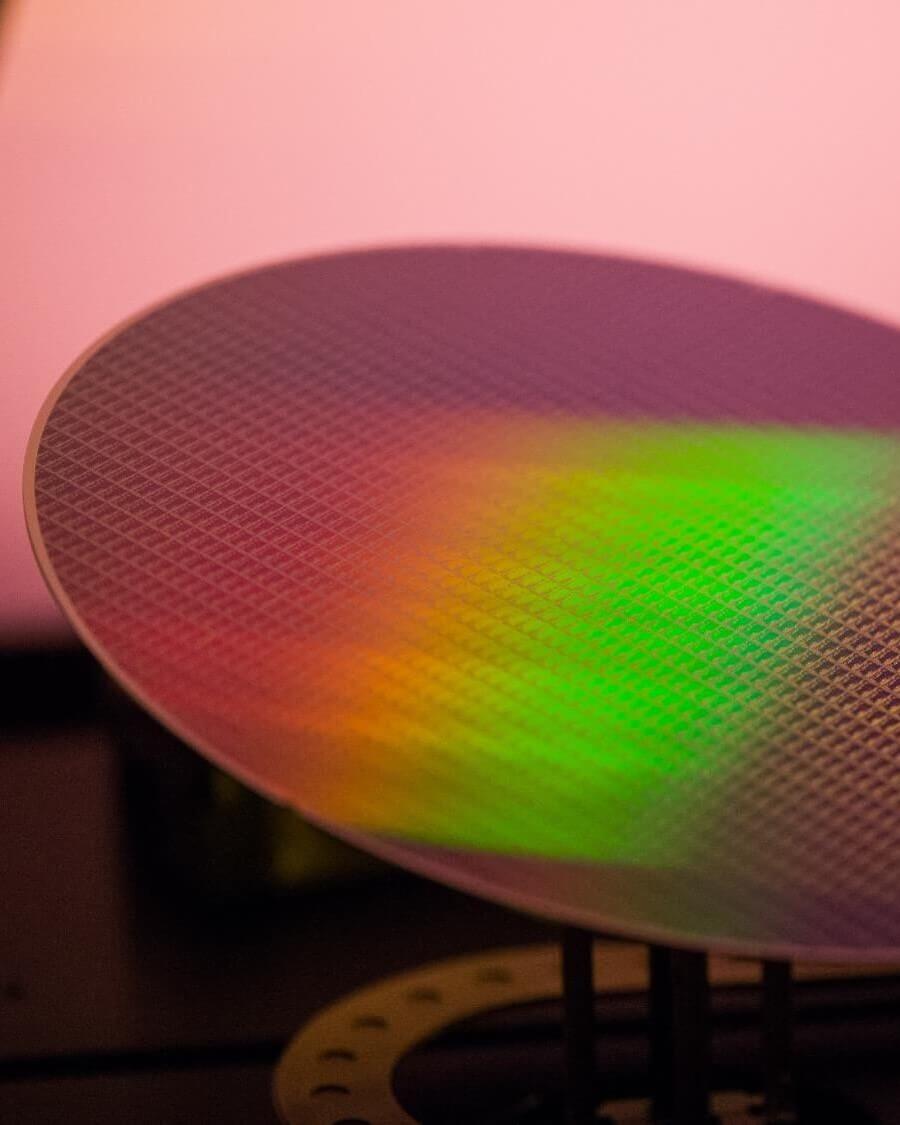
Robust Operations to Support Even the Most Complex Equipment
Semiconductor manufacturing equipment must be finely calibrated to support the intricate work involved in producing sophisticated components. Shyft’s service capabilities and routine processes cover testing, certification, reporting and root cause analysis, which are vital to ensuring equipment performance, safety and reliability.
-
With technicians trained to test, analyze and repair nearly any type of technology, we work to verify that the equipment’s core functions, features and operational capabilities are working as specified for the production environment in which they’re deployed.
Shyft’s device troubleshooting ensures thorough testing and proper repairs, and we offer custom test fixture creation for solid troubleshooting, as well as customer support and manufacturing feedback.
-
Together, Shyft’s highly trained experts, global infrastructure, high-efficiency operational models and proprietary shop floor control system mean your customers get the best from their technology investments even long after the initial sale. Our services are performed in alignment with OEM requirements to mitigate risk, maintain equipment warranties and extend OEM support eligibility as equipment ages.
We operate to numerous industry standards, including:
- ISO 9001:2015 Quality Management Systems
- ISO 14001:2015 Environmental Management Systems
- Cleanroom operated to ISO 5/Class 100 standards (California)
-
Detailed, actionable reporting and documentation helps with quality control and increases visibility into service activities, uncovers trends and empowers OEMs to make well-informed decisions. Our unbiased observations and analyses provide invaluable feedback to customer manufacturing and support organizations, and impact the way future products are designed, manufactured, tested, repaired and handled in the field and logistics processes.
-
Across all services, Shyft focuses on a variety continuous improvement initiatives to enhance overall customer and end-user satisfaction by enabling a consistent and predictable level of quality over time. This helps to reduce downtime and enable a lower cost of operation.
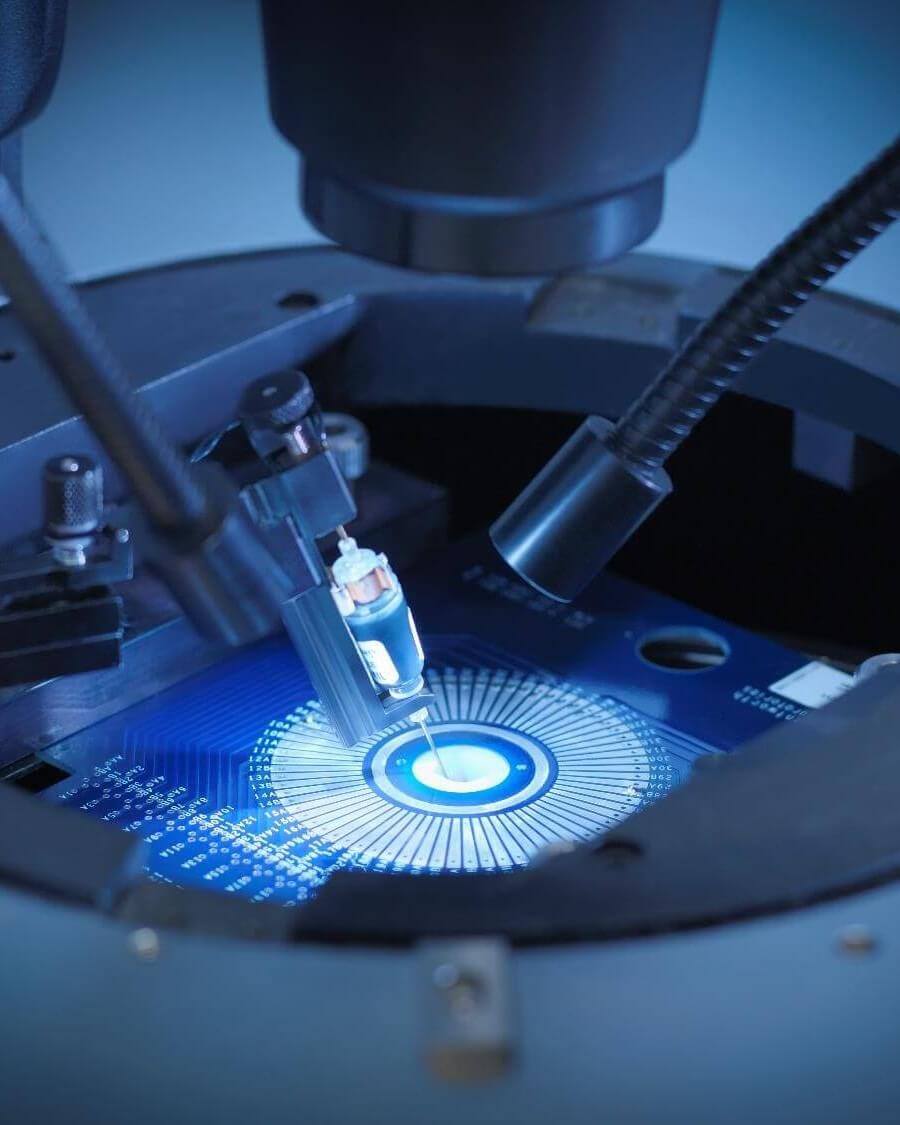
Decades of Technology Service Know-How and Experience
When it comes to semiconductor equipment manufacturing, the pace of innovation, increasing complexity, faster obsolescence and sky-high customer and stakeholder expectations are always critical business considerations. Equipment manufacturers must consistently adopt the latest technologies while maintaining product quality, operational efficiency and profitability. This not only requires robust agility, but also extensive and deep technical know-how of your team and your service partners alike.
-
Shyft engineers are skilled experts in root cause analysis and failure data. Root cause and failure analysis at the board level can ensure fast, accurate repairs and provide unbiased feedback that can be used to improve designs, reduce failure rates and increase product longevity.
-
The global shortage of engineers, technicians and other highly skilled professionals is felt deeply across the technology industry. As generations with decades of experience retire, they are simply not being replaced in the workforce at the same rate.
Fortunately, Shyft’s engineers and technicians are on standby with in-depth knowledge of semiconductor manufacturing equipment and they utilize state-of-the-art tools, proprietary software and OEM-certified spare parts to repair equipment and instruments in controlled cleanroom environments.
-
Shyft engineers are experienced in supporting customers with remote diagnostic services to help troubleshoot or even perform some calibration prior to shipping equipment in for repair. Our remote support capabilities include:
- 24x7x365 support
- Levels 1, 2 and 3 support
- Robust mix of product parts, labor and technical expertise
-
Shyft allocates significant resources to ensure the skills, tools, environments, processes and other necessities are in place to support semiconductor manufacturing equipment through rapid innovation and long product lifecycles. This includes but is not limited to:
- Cleanroom-compatible tools for disassembling and reassembling equipment
- Vibration isolation tables for working with sensitive components like optics and sensors
- Tools for working with high-precision robotic systems and motion stages
- BGA removal and replacement equipment
